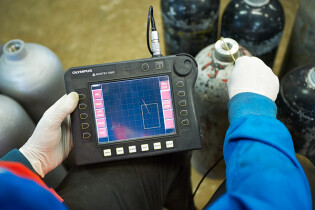
Periodic testing of gas cylinder to TPED, UKAS and DOT accredited standards.
All compressed gas cylinders have to be hydrostatically tested every 10 years to ensure they are safe and fit for purpose. Gielle has in-house test facilities to enable us to carry out cylinder testing. We hydrostatically test and maintain fire suppression cylinders, liferaft cylinders and BA cylinders to both TPED, UKAS and American DOT standards.Hydrostatic testing involves the cylinder being filled with water and placed inside a water-filled high-pressure chamber. Water pressure inside the cylinder is increased (150% of maximum working pressure) causing the cylinder to expand slightly.
This in turn displaces a small amount of water from within the chamber, which is collected and measured. If the cylinder expansion is within regulation limits (< 5%), then the cylinder has passed and can be certified fit for purpose. Compliant cylinders are dried out, stamped as tested with the current month and year, refilled with the appropriate suppression agent and placed back in service. Failed cylinders must be destroyed.